- Home
- Blog
- Plastic Polymer Composite Article
- Full Guide to the Blown Film Process: From Plastic Pellets to Film Products for Industrial Applications
Full Guide to the Blown Film Process: From Plastic Pellets to Film Products for Industrial Applications
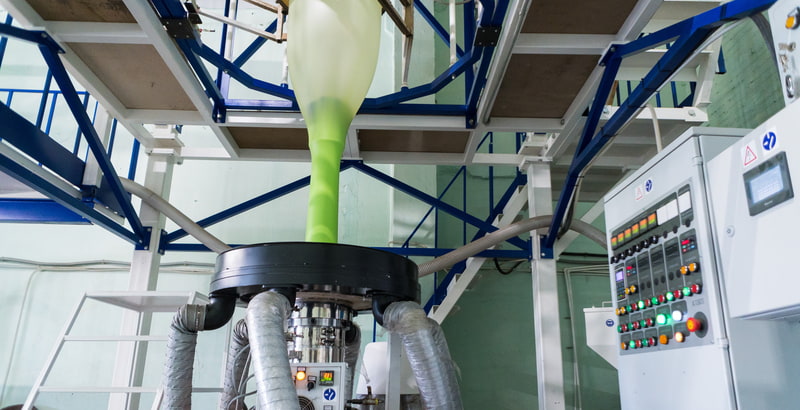
Did you know that many plastic products in our daily lives are made using blown film technology? Products such as industrial stretch film, shrink film, and pallet wrap are all types of blown film products. These products feature high extensibility, strong toughness, and excellent puncture resistance, and they can also have adjustable thickness. Additionally, blown film machines for zipper bags are particularly suitable for various packaging needs in food, accessories, and electronic consumables. If you want to customize blown film products, the key lies in the core material of the blown film process— Calcium Carbonate Masterbatch and CaCO3 Filler—and the plastic processing methods. This article will guide you to fully understand this technology!
〈Extended Reading:What is Extrusion? Principles, Applications, and Its Benefits for Long Plastic Products〉
What is Blown Film?
Blown film is a type of plastic product made using the blown film process, a common plastic processing method. It involves heating and melting plastic pellets, which are then inflated with air to form a film. The process typically starts with the extrusion of the polymer to form a thin-walled tube, which is then inflated to the desired thickness using high-pressure air, finally cooled and solidified into a film.
Characteristics of Blown Film
Plastic film is a common plastic product, typically made through processes such as calendering, extrusion, or blow molding. The blown film process involves melting plastic raw materials in an extruder, forming them into a thin tube, and inflating it with compressed air. Finally, it is cooled and shaped to form the film product. The film products made through this blow molding process have the following characteristics:
-
Durability: After stretching and inflating, they possess higher mechanical properties, tensile strength, and toughness, making them less prone to breaking.
-
Cost savings: The products have no scrap material and minimal waste, significantly reducing production costs.
-
Excellent barrier properties: Plastic products made by blow molding can effectively block air, water vapor, and other elements.
-
Production flexibility: Blown film has a wide range of applications, with fewer seams, making subsequent processing (such as s sealing and bag-making making) very convenient.
-
Consistent thickness: The thickness of the film can be precisely controlled, and when combined with high-quality plastic masterbatch, it can ensure greater process stability.
〈Extended Reading:A Comparative Study of PVC Compound and Masterbatch: Key Materials in Plastics Processing〉
What are The Uses of Blown Film? Examples of Applications From Industry to Daily Life
Industrial Field
The blown film process can produce various industrial pipes. Rigid pipes are commonly used for transporting liquids and gases, such as chemical pipelines, drainage pipes, and cable conduits. Flexible hoses, due to their soft and bendable characteristics, are widely used in medical devices, cable sheaths, and other fields.
Transportation Protection
The blown film process can also produce transportation packaging materials such as bubble cushioning pads, tamper-evident courier bags, bubble wrap, and protective films. These plastic films or bags can prevent items from being exposed or falling during transportation. Processed bubble cushioning pads and bubble wrap can tightly wrap products, serving as a protective layer to reduce collision damage during transit, ensuring that items are safely delivered.
〈Extended Reading:Application of Calcium Carbonate Masterbatch in the PE Buffer Packaging Material Industry〉
Medical Applications
Through the blown film process, medical supplies such as medical waste disposal bags, collection bags, medication bags, and disposable aprons can be produced. Due to the excellent isolation properties of plastic films and bags, they are commonly used to store hazardous waste and collected materials, preventing cross-contamination while keeping invasive surgical supplies clean, thus ensuring the safety and hygiene of the medical environment.
Agricultural Field
Common blown film products include greenhouse films and ground cover films. Greenhouse films are used to construct greenhouses, which can regulate the temperature and humidity inside, helping crops grow better and increasing yields. Ground cover films can prevent pests, suppress weeds, and also prevent soil erosion, reducing the use of fertilizers and herbicides, lowering labor and material costs, and enhancing harvests. They are essential tools in organic farming!
〈Extended Reading:The application of Calcium Carbonate Masterbatch in Agricultural Mulch Film〉
Construction Field
Current building materials often have insufficient insulation, frequently requiring high-energy-consuming air conditioning to maintain indoor comfort, with about 60% of heat energy entering indoors through thermal radiation. Multi-layer plastic film technology is widely used for transparent insulation in the market, with its transparent plastic structure available in films and panels, commonly made from materials like PC, PE, and PET. This blown film technology can be applied in building windows, skylights, curtains, etc., allowing for the use of natural light to create a bright and comfortable indoor environment while saving on lighting and air conditioning electricity. It significantly contributes to energy conservation, carbon reduction, and mitigating global warming effects!
Food Packaging
Blown film products are very common in food packaging, such as heat-resistant bags, plastic cup sealing films, bread bags, and self-adhesive cookie bags. They are soft and offer excellent sealing properties. For example, when marinating or storing food, using ziplock bags can reduce the hassle of cleaning, as they are lighter and save space compared to glass containers. They are suitable for various solid and liquid foods, making storage and transportation convenient and helping to extend the shelf life of food.
Daily Household Use
Everyday household blown film products include zip lock bags, garbage bags, disposable tablecloths, and disposable gloves, making cleaning tasks super convenient. These disposable blown film products effectively prevent direct contact with dirt or chemicals, making household chores easier and more efficient.
〈Extended Reading:The Application of Calcium Carbonate Masterbatch in the Plastic Bag Industry〉
How is Plastic Film Manufactured? An Overview of the 5 Key Blown Film Processes
The process of making plastic film is quite similar to blowing bubbles. The blown film machine mimics the process of blowing bubbles on a tower production line, but instead of soapy water, it uses plastic polymers. The blown film bubble is then pressed into an extremely thin film. The height of the tower structure can be adjusted according to needs, and once the film is formed, it is rolled up for easy distribution and transportation to the end market.
Step 1: Polymer Mixing
The primary raw materials for blown plastic films include LDPE, HDPE, LLDPE, EVA, PVC, PP, PS, and PA. When the plastic polymers enter the machine, they are first evenly mixed with additives and fillers (such as calcium carbonate masterbatch and talc masterbatch) in the mixing barrel, and then sent to the extruder. The extruder heats the materials until they melt, ensuring the uniform incorporation of additives such as antistatic agents, adhesives, and UV stabilizers.
Step 2: Bubble Formation
When the polymer is completely melted and evenly mixed with additives, it is extruded from the extruder and enters the next stage - the blown film die. The blown film die is located above the rear end of the extruder and is designed in a circular shape. As the molten polymer passes through the die, an air ring blows air into it, causing the extruded material to expand and form a tubular bubble, and then can be shaped into a film structure.
Step 3: Inflation and Cooling
The bubble stabilizer frame helps keep the film bubble stable after expansion; it surrounds the bubble to maintain its shape. Some blown film machines are equipped with an Internal Bubble Cooling (IBC) system, which accelerates the cooling process, allowing the molten polymer to rapidly transition from a liquid to a solid state. When the blown film bubble reaches its optimal state, the next step of pinching can be performed, ensuring the quality and uniformity of the thickness of the finished product.
Step 4: Flattening the Film Bubble
The tube collapsing frame and nip rollers, located at the top of the blown film machine, guide the film bubble to the nip rollers, where it is flattened into a thin film. The high-quality blown film materials produced by professional blown film machines are suitable for various types of film packaging, offering excellent barrier properties that effectively preserve freshness, prevent moisture, and resist frost. They also block oxygen and are oil-resistant, ensuring the quality and safety of the packaged contents.
Step 5: Winding the Film into Rolls
In the final stage of the blown film process, the film is collected by the winding machine. The recoiling machine consists of large rollers that evenly wind the film. To ensure the quality of the film, the recoiling machine's speed must be synchronized with the nip rollers to avoid unnecessary stretching or deformation. After winding, the film is organized into rolls, ready for transportation or further processing applications.
The Key to Enhancing the Quality of Blown Film Quality - Calcium Carbonate Masterbatch
Calcium carbonate masterbatch is driving a new trend in the blown film industry. Calcium carbonate is a natural inorganic salt powder and is the most commonly used natural non-toxic filler in industry. Adding calcium carbonate can reduce the use of plastic raw materials, decrease resource waste, and lessen environmental impact, playing an important role in the modern plastic products industry! Next, let’s explore the advantages of APEX calcium carbonate masterbatch in blown film applications:
〈Extended Reading:What is Calcium Carbonate? A Comprehensive Guide to Its Production, Types, and Applications!〉
Increase Smoothness
As a professional inorganic powders manufacturer, APEX provides stable and precise powder specifications that effectively enhance the smoothness and flatness of plastic bags. In addition to improving smoothness, calcium carbonate masterbatch can significantly increase the compressive strength and wear resistance of plastic products, minimize shrinkage issues and prevent deformation, thereby enhancing the overall performance and durability of the products.
Enhance Aesthetics
For filling materials, it is recommended to use ultrafine calcium carbonate, with particle sizes uniformly ranging from 1.8 to 3.3 μm. This type of calcium carbonate can make the surface of blown film plastic products smoother, further enhancing the tactile feel and quality, providing a better user experience, and making the shopping and packaging process more convenient. Additionally, it enhances bag durability and printing clarity, making the products more aesthetically pleasing in daily use and meeting high-quality packaging demands.
Low Production Cost
Calcium carbonate is a natural, non-toxic additive with relatively low costs, and the filling ratio can reach 75% to 88%, effectively reducing the production costs of blown film plastic products. This not only reduces dependence on costly raw materials but also optimizes cost-effectiveness while maintaining product performance and quality—making it a major advantage for manufacturers!
Conclusion
The quality of blown film products is crucially dependent on the plastic polymers and additives used. APEX calcium carbonate masterbatch features stable components and high-quality powder specifications, which can effectively enhance the smoothness, compressive strength, wear resistance, and aesthetics of blown film products. It also significantly reduces production costs, achieving the perfect balance between performance and aesthetics. Contact us now to learn how APEX calcium carbonate masterbatch can help you optimize your blown film products and enhance your market competitiveness!
〈Extended Reading:Comprehensive Guide to Industrial-Grade Talc Powder:Properties and Advantages in Applications〉
〈Extended Reading:What is Extrusion? Principles, Applications, and Its Benefits for Long Plastic Products〉
Article Classification
Recent Articles
- A Complete Guide to Polypropylene (PP): Properties and Applications
- What Is PE Plastic? A Complete Guide to Its Types, Properties, Advantages, and Applications
- What Are Plastic Fillers? The Application and Tips for Choosing the Right One
- Full Guide to the Blown Film Process: From Plastic Pellets to Film Products for Industrial Applications
- What Is Injection Molding? Applications, Processes, and Key Products Explained!