- Home
- Blog
- Plastic Polymer Composite Article
- What is Filler Masterbatch? Explanation of the Filler Masterbatch Process and the Applications of Calcium Carbonate Masterbatch
What is Filler Masterbatch? Explanation of the Filler Masterbatch Process and the Applications of Calcium Carbonate Masterbatch
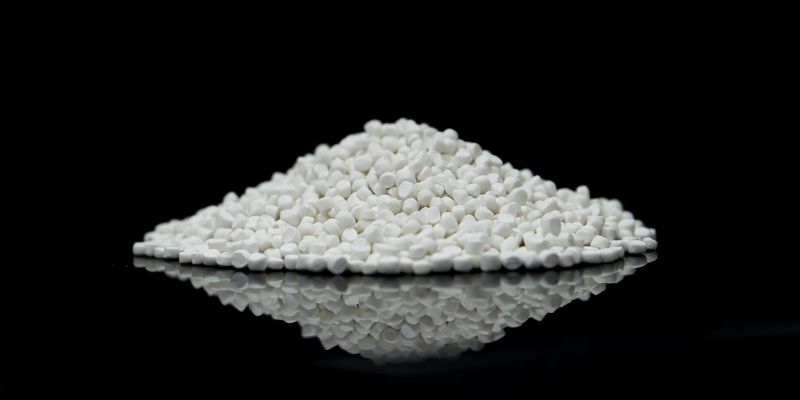
The Calcium carbonate masterbatches in filler masterbatches are known for their high whiteness, which makes suitable for various colored products. Their excellent dispersibility and heat resistance contribute to enhancing the heat durability and maintaining the hardness of products, while reducing the amount of plastic used, thus lowering material costs. This article will delve into the definition, manufacturing process, and filling materials of filler masterbatches, as well as their advantages and applications in plastic products.
What is Filler Masterbatch?
Calcium carbonate masterbatches are composed of calcium carbonate powder, a portion of base resin, and plastic additives. These components melt into a liquid at high temperatures and are then extruded into small plastic granules through an extruder. These masterbatches are widely used as fillers in plastic products, replacing part of the raw materials to reduce costs while enhancing product functionality. The calcium carbonate powder typically constitutes 60% to 90% of the mixture and is compatible with polyolefin resins (such as PP, PE). It can also be mixed with other plastics, such as polystyrene (PS), ABS resin, polyvinyl chloride (PVC), and expandable polystyrene (EPS), providing an economical solution for the plastics industry.
What Fillers are Used in Filler Masterbatches?
The composition of filler masterbatches significantly affects the hardness, strength, abrasion resistance, and the overall quality of plastic products. Generally, filler masterbatches consist mainly of carrier resin, fillers, and various additives, with the fillers being the principal component, comprising up to 90% of the content. The composition of calcium carbonate masterbatches will be introduced in detail below:
1. Calcium Carbonate Powder (Comprising 70-90% of the Content)
Filler masterbatches are composite materials consisting of multiple components, primarily consisting of a carrier resin, fillers, and various additives, with the filler content reaching up to 90%! Among these, calcium carbonate powder is the most significant filler, followed by inorganic fillers such as kaolin, chalk, and talc. Filler masterbatches that incorporate calcium carbonate typically use low-density polyethylene or linear low-density polyethylene as the basic material, forming a high-concentration plastic modifier. This high-quality plastic modifier can reduce plastic usage and ensure product performance. With an average particle size of 2.0μm, the filler content is usually between 75% to 85%, offering good dispersibility and heat resistance, which helps to enhance the hardness of the plastic, the stability of product dimensions, and prevents any deformation or shrinkage due to external factors.
2. Carrier Resin
Although the carrier resin constitutes up to 20% of the filler masterbatch content, it is a key factor affecting its performance and cost. Ensuring the compatibility of the carrier resin with the base plastic matrix resin to achieve proper mixing and performance. Additionally, the melting point of the carrier resin should match that of the matrix resin to avoid processing issues. Commonly used carrier resins include polypropylene (PP), polyethylene (PE), and a blend of polyethylene and polypropylene with a similar Melt Flow Index (MFI). These resins have good processability and compatibility, ensuring more stable quality and cost-effectiveness in the manufacturing process of calcium carbonate masterbatches.
The Process of Filler Masterbatch Production
With changes in the components of the carrier resin, the processing technology and related equipment for filler masterbatch will also be adjusted accordingly. Generally speaking, the manufacturing process of the filler masterbatch can be divided into the following four stages:
Filler Masterbatch Production Process 1: Mixing Components
In the first stage of the filler masterbatch production process, calcium carbonate powder, base resin, and additives are placed into the machine for high-speed mixing. This process ensures that all components of the calcium carbonate masterbatch is evenly blended, laying the foundation for subsequent processes.
Filler Masterbatch Production Process 2: Melting and Mixing the Mixture
The mixture is heated to a high temperature until it melts into a liquid state, after which it is kneaded and dispersed into pellets. This step ensures that the mixture is evenly blended and forms a homogeneous filler masterbatch material for further processing.
Filler Masterbatch Production Process 3: Extrusion
The kneaded mixture clump is fed into a screw extruder, where it is pressed through a mold to create strands, ensuring that the filler masterbatch is extruded evenly and shaped according to requirements, preparing it for subsequent processing steps.
Filler Masterbatch Production Process 4: Cut into Pellets
After the extrudate is cooled and solidified through air or water cooling, it is cut into granules using a cutter or pelletizer. These granular filler masterbatches are added to other resins, imparting new characteristics to the base plastic and thereby affecting the performance of the final product.
Applications of Calcium Carbonate Masterbatch
PP (polypropylene) masterbatches and PE (polyethylene) masterbatches are types of calcium carbonate masterbatches. The application of calcium carbonate masterbatches in the manufacture of plastic products is primarily focused on injection molding. When calcium carbonate masterbatch is mixed with PP resin, the calcium carbonate content can be as high as 50%. This blend provides excellent thermal conductivity, impact resistance, hardness, flexibility, and reduced shrinkage rate. These properties make it widely used in the production of various household items.
In addition to mixing with PP (polypropylene) and PE (polyethylene), calcium carbonate masterbatch can also be mixed with PS (polystyrene) plastic. Overall, the use of calcium carbonate masterbatch offers benefits such as enhancing the hardness of plastics and reducing the cost of plastic materials. Since calcium carbonate masterbatch is a natural mineral, it can reduce dependence on petroleum-based raw materials, making it a more sustainable and environmentally friendly plastic base material. Here are five common applications of calcium carbonate masterbatch:
Calcium Carbonate masterbatch Application 1: Blown Film Products
Adding calcium carbonate masterbatch improves the rigidity and durability of the film, making it suitable for various packaging applications, including food packaging and agricultural films. Additionally, calcium carbonate masterbatch can increase the processing performance of the film and increase production efficiency.
Calcium Carbonate masterbatch Application 2: Plastic Pipes
The addition of calcium carbonate masterbatch can significantly improve the hardness and tensile strength of plastic pipes, increase their pressure-bearing capacity, and reduce the cost of the pipes at the same time. This modification can increase the durability and stability of plastic pipes, making them suitable for applications in construction, drainage, and other fields.
Calcium Carbonate masterbatch Application 3: Plastic Sheets
The addition of calcium carbonate masterbatch strengthens plastic sheets more robust and enhances their surface gloss, making them suitable for use in construction, billboards, and other areas. Calcium carbonate masterbatch can also be used in the production of various plastic products, such as PP (polypropylene) plastic sheets and PE (polyethylene) plastic sheets, with a wide range of applications.
Calcium Carbonate masterbatch Application 4: Injection molded products
Adding calcium carbonate masterbatch during the injection molding process can produce injection-molded products with high hardness and strong compression resistance. These products are widely used in various fields, such as home appliances and automotive parts. Moreover, calcium carbonate masterbatch is also suitable for various processes, including injection molding, extrusion, and drawing, etc.
Calcium Carbonate masterbatch Application 5: Extruded products
Applying calcium carbonate masterbatch to the extrusion process can enhance the surface hardness of extruded products, commonly found in flexible conduit. This method makes the products more robust and durable, while also reducing manufacturing costs. It is extensively used in various plastic products that require high strength and hardness.
The Features of APEX Calcium Carbonate Masterbatch
1. Excellent dispersibility and compatibility: APEX Calcium Carbonate Masterbatch features excellent dispersibility and compatibility, effectively bonding with polyethylene (PE) and polypropylene (PP) substrates. This ensures even dispersion in plastic products and enhances overall product quality.
2. High whiteness: It features high whiteness, suitable for manufacturing products in various colors and meeting the diverse needs of different customers.
3. Improves heat resistance: It enhances the product's heat resistance, thereby increasing the product's durability and lifespan.
4. Increases hardness: Adding it increases the hardness of plastic products, making them sturdier and more durable.
5. Reduces plastic usage and lowers costs: The high concentration of calcium carbonate filler in the masterbatch allows for a reduction in the amount of plastic used in the manufacturing process, thereby lowering material costs.
6. Enhances dimensional stability and prevents secondary pollution: It enhance the product's dimensional stability, reduce heat generation, and prevent secondary pollution during the combustion, meeting environmental protection requirements.
7. Complies with environmental standards: The product meets ROHS 2.0 and SGS standards for testing of eight heavy metals, indicating a higher level of environmental friendliness.
( Please refer to our Filler Masterbatch product introduction . )
Common Questions of Filler Masterbatch and Calcium Carbonate Masterbatch
Filler masterbatches play a crucial role in the manufacturing of plastic products, effectively reducing production costs and enhancing product performance. However, during the production of calcium carbonate masterbatches, we often encounter challenges such as dispersion, fluidity, cost control, plasticization, and weather resistance. To ensure smooth production and high-quality products, this article will explore these common issues in depth.
Q1: How to Choose a Filler Masterbatch Manufacturer?
When choosing a filler masterbatch manufacturer, the first thing to consider is the raw materials they use. For example, APEX calcium carbonate masterbatches are made from high-quality minerals to ensure stability and reliability. Secondly, focus on their precision in craftsmanship to ensure that the calcium carbonate is evenly dispersed within the filler masterbatch, which enhances the product performance. Additionally, the manufacturer should offer customized solutions to meet the needs of various application areas. Lastly, environmental sustainability is also an important consideration. Choosing a manufacturer that adheres to eco-friendly principles can help reduce the demand for traditional plastic materials and minimize the environmental impact.
Q2: How to Determine the Filling Effect?
The key to determining the filling effect lies in the particle size and distribution of the inorganic fillers. Generally, the smaller the particle size and the narrower the distribution, the better the filling effect. Additionally, the filling effect is related to the dispersibility of the filler; the smaller the particle size, the more difficult it is to disperse, but the better the filling effect. However, filler masterbatches with smaller particle sizes are usually more expensive. Furthermore, when choosing a carrier for the filler masterbatch, its melting point and fluidity should be considered. The melting point of the carrier resin should not be higher than that of the base resin to ensure the stability of the production process.
Q3: What is the Difference between Filler Masterbatches and General Plastics?
General plastics are pure polymer chains without any other components. Filler masterbatches, on the other hand, are composite materials made up of multiple components, with calcium carbonate powder being the most important component, typically comprising 70-80% of the filler masterbatch content. Manufacturers can add pigments or other additives according to customer needs to improve the quality of plastic products while reducing production costs at the same time.
Q4: How Do Filler Masterbatches Achieve 'Plastic Reduction'?
The high concentration of calcium carbonate fillers in the filler masterbatches can be added during the plastic manufacturing process to reduce the amount of plastic used. With the establishment of the Global Plastics Treaty, the issue of plastic reduction significantly impacts the plastic industry. Companies must aim to 'control the life cycle of plastics', reducing the use of plastic materials from the source. In the future, the 'plastic tax' of various countries must be considered in product exports. Therefore, incorporating filler masterbatches into plastics, allowing calcium carbonate to replace some of the plastic, is an indisputable solution to help companies achieve their plastic reduction goals.
Conclusion
Calcium carbonate powder is the primary component of filler masterbatches. When mixed with plastic raw materials, it enhances the hardness, strength, and abrasion resistance of the product. Additionally, because calcium carbonate masterbatches can replace part of the plastic and extend the usage cycle of plastic products, they have become a significant force in helping enterprises achieve their plastic reduction goals. APEX is committed to providing high-quality filler masterbatches. High-quality calcium carbonate masterbatches require not only advanced technology and equipment but also a strict quality control system. We have multiple advanced technology machines from Taiwan, to ensure efficient and stable production capacity, and we strictly follow international standard testing items. If you have any needs for filler masterbatches or calcium carbonate masterbatches, please contact us .
Article Classification
Recent Articles
- A Complete Guide to Polypropylene (PP): Properties and Applications
- What Is PE Plastic? A Complete Guide to Its Types, Properties, Advantages, and Applications
- What Are Plastic Fillers? The Application and Tips for Choosing the Right One
- Full Guide to the Blown Film Process: From Plastic Pellets to Film Products for Industrial Applications
- What Is Injection Molding? Applications, Processes, and Key Products Explained!